Protecting Feed & Grain Processing Facilities from Explosions
Managing risks of explosion through venting, suppression and isolation.
breadcrumb >> list
Article reprinted from IEP Technologies link
Dangers Inherent in Grain & Feed Processing
Every feed and grain processing facility is a candidate for a devastating explosion, simply because all the elements are present, all the time. These conditions include fuel in the form of finely divided combustible dust; an ignition source which can range from a welding spark to a lightning strike; an oxidizing agent, which is typically the oxygen in the air; confinement that causes a pressure buildup; and dispersion of the dust into the airstream. When all these elements come together, your company is at risk of putting your people and processes in danger, not to mention creating negative headlines in the press and trade publications.
In feed and grain plants, the process equipment most typically associated with dust explosions includes: dust collectors, mills, storage hoppers or silos, and bucket elevators. All of these vessels can have grain dust in suspended form, either during normal operations or in an upset condition. Once the grain dust is suspended into a dust cloud, all it takes is an ignition source to initiate the deflagration. The pressure from a deflagration travels at the speed of sound, while the growing fireball initially propagates at a much slower speed.
How Dust Explosions Happen
A typical sequence for a dust explosion includes:
- Ignition of the dust cloud
- The deflagration pressure results in rupture of the vessel
- The shock wave from this ruptured vessel liberates dust that has accumulated on horizontal surfaces in the process area, such as atop beams, ducts, conveyors and even light fixtures, causing it to become suspended in the process area
- The escaping fireball from the initial process vessel ignites the newly suspended dust in the process area, causing a secondary explosion that can destroy the building
- Flame propagation occurs through interconnected ducts, chutes or conveyors to connected equipment upstream and/or downstream, with the resulting secondary explosions.
Explosion Risk Management
DHA - Dust Hazard Analysis
Managing this explosion risk requires a comprehensive understanding of the normal, abnormal and upset conditions in the processing equipment. The National Fire Protection Association (NFPA) suggests that a Dust Hazard Analysis (DHA) be performed. This includes an assessment of the combustible properties of the dust being handled, identifies where a dust cloud can occur in the process, and determines likely ignition sources. The DHA should evaluate the consequences of a deflagration, including both primary and secondary explosion scenarios. Another critical part of a DHA is identifying explosion prevention and mitigation steps that should be taken to reduce the risk of an incident.
A DHA will focus on areas of a facility that historically exhibited the highest likelihood of experiencing a deflagration. In an agricultural processing facility, these include:
Mechanical Transfer Equipment
Bucket elevators, drag conveyors and screw conveyors are common ignition threats within the facility. The risk of frictional heating due to wear or misalignment could result in smoldering or burning embers that are transmitted downstream. While in a layer form, these embers are a fire risk. At the transfer points, such as the discharge from an elevator head, the burning embers can be introduced into a dust cloud, where all of the conditions are correct for an explosion.
Particle Size Reduction
Mills, grinders and pulverizers mechanically reduce the size of the product. The ignition risk from this equipment is one of the highest inside a processing facility due to frictional heating. Introduction of foreign material or attrition of the milling equipment itself can create ignition sources. Often the mill is substantially built to withstand the overpressure of a low-grade explosion; however, flame propagation to interconnected equipment causing a secondary explosion is likely.
Dust Collection
Within the facility, generally the finest dust is found in the dust collection system. The finer the dust, the lower the amount of ignition energy needed to ignite it. Also, the finer the dust from a specific solid material, the higher its explosivity characteristics tend to be. Compounding these threats are the fact that dust collectors are connected to one or more vessels upstream, with a high risk of flame propagation and the resulting secondary explosion in connected vessels. These factors make dust collectors one of the greatest explosion risks in the plant.
Storage
Material handled in material transfer systems, particle size reduction, and often dust collection usually ends up in a storage vessel such as a bin, hopper or silo. An ignition source generated upstream may not find the right dust cloud conditions until it is dropped into the storage vessel, where the explosion then occurs. Also, it is not uncommon for multiple storage vessels to be interconnected either through the feed system or through dust extraction, leaving a path for flame propagation from one vessel to the next.
Explosion Prevention
The first line of defense should be explosion prevention. This includes measures to minimize ignition source potential. Typical ignition sources include bearing failure/overheating, electrostatic discharge and mechanical failure of product or airmoving equipment. Ignition prevention techniques commonly used are strategically placed magnetic separators, bearing temperature monitors, and electrostatic bonding and grounding. Minimizing the residual dust layers on horizontal surfaces is an important part of any explosion prevention program. Diligent housekeeping to prevent the accumulation of dust outside the process equipment will reduce the risk that an explosion in a process vessel will result in a secondary explosion that destroys the facility.
Three effective means of explosion mitigation
Ignition control, proper housekeeping of residual dust and continuous safety training of plant personnel are all critical to help prevent an explosion from occurring under normal operating conditions. Unfortunately, abnormal conditions that result in an explosion can occur in any process line. This is why NFPA 61 (Agricultural and Food Processing Facilities) and NFPA 652 (Fundamentals of Combustible Dust) require the use of explosion mitigation techniques for vessels subjected to an explosion threat. NFPA 68 (Deflagration Venting) and NFPA 69 (Explosion Prevention Systems) lists a number of different mitigation methods that can be employed to deal with an explosion threat. The most common techniques include explosion venting, explosion suppression and explosion isolation.
Explosion Relief Venting
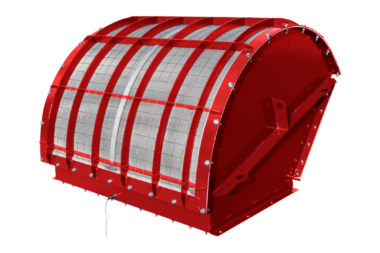
Explosion Relief Venting is one of the most widely used methods for mitigating dust explosions. It requires an explosion relief vent installed on the wall of a process vessel. The vent features a membrane constructed of a material weaker than the vessel wall. During a dust explosion’s incipient stage, the vent ruptures and directs the explosion’s overpressure, flame, burnt and unburnt material, and other combustion by-products away from the vessel to a safe location. The explosion relief vent is designed to ensure that the explosion’s pressure rise doesn’t exceed the vessel’s pressure shock resistance. These vents are designed according to procedures in NFPA 68: Standard on Explosion Protection by Deflagration Venting. NFPA provides an equation for estimating the vented fireball’s size and from this information, you can calculate the safe distance required in front of the vented vessel to protect workers, equipment and the building structure from the ejecting fireball.
Flameless venting protects indoor equipment from dust explosions by combining an explosion relief vent with a mesh trap that arrests flame and retains particles. Like an explosion relief vent, the flameless vents sealing device (either a spring-loaded disc or a rupture panel) during a deflagration. The deflagration’s overpressure, flame and material discharge through the mesh trap, which prevents the flame from discharging into the surrounding area. Instead, the flameless vent discharges hot gas and overpressure. A safety perimeter must be established around the flameless vent to protect workers from this discharge.
It is important to understand that explosion venting only relieves the deflagration pressure from the protected vessel. It does not stop flame from propagating to any interconnected vessel, nor does it address the post-explosion fire in the vented vessel. Other protection measures are needed to deal with these threats.
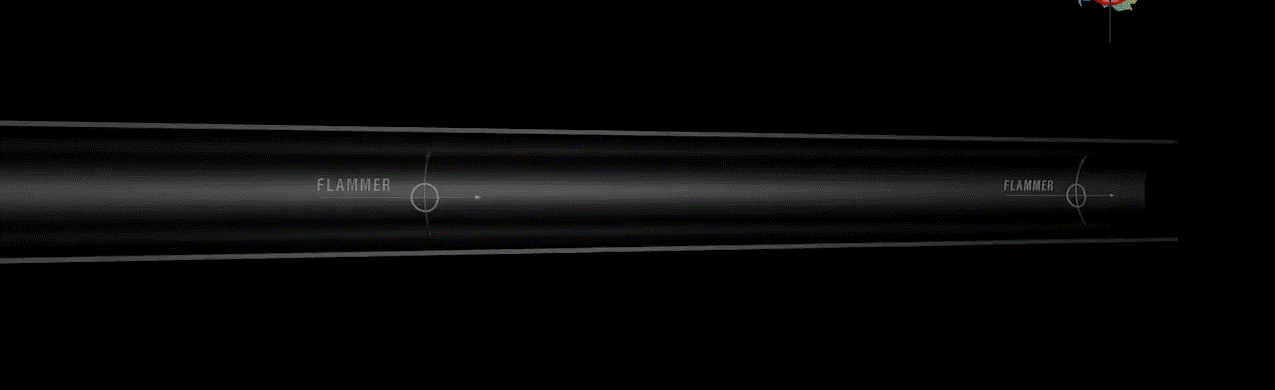
Explosion Suppression Systems
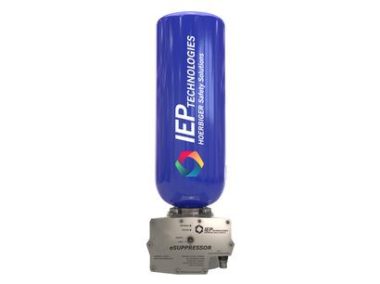
Explosion Suppression Systems are often installed in applications where it is not possible to safely vent an explosion away from process equipment. The system detects an incipient dust explosion very soon after ignition and discharges a chemical extinguishing agent quickly enough into the developing fireball inside the equipment to extinguish the deflagration before a destructive overpressure develops. Explosion suppression systems are designed according to NFPA 69: Standard on Explosion Prevention Systems. Typically, explosion suppression systems also include explosion isolation for interconnected ducts through which flame propagation may occur.
The major advantages of explosion suppression are that no flame is ejected from the protected vessel, and the risk of a post-deflagration thermal event is greatly diminished.
Explosion Isolation Devices
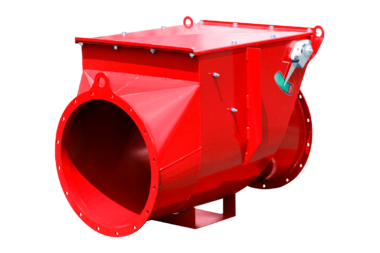
Explosion Isolation Devices prevent a deflagration in a process vessel from propagating through a connection such as a duct, chute or conveyor to other equipment, where it could cause subsequent explosions. The devices work by mitigating the flame propagation and pressure piling between connected equipment. An isolation device can be active or passive. An active device has detection components, including explosion pressure and/or flame detectors, and a control unit. The detectors detect explosion pressure or a flame and send a signal to the controls to rapidly deploy the device. These active explosion isolation devices are either chemical or mechanical. A chemical isolation device works by rapidly discharging a chemical extinguishing agent, such as sodium bicarbonate, into connecting ductwork to mitigate flame propagation. A mechanical isolation option includes a high-speed gate valve. Milliseconds after the active high-speed gate valve’s detectors sense explosion pressure or flame, the controls rapidly deploy a mechanical barrier — closing the valve’s gate across the connecting ductwork.
In addition to the active isolation options, there are passive isolation means available to mitigate flame propagation. The passive valve, which can have a flap or float, is self-actuated by the airflow from a deflagration so it requires no detectors or controls. This device is typically used to isolate dust-handling equipment with relatively low dust loads.
Summary
Dust explosions at feed and grain handling facilities do not need to happen. Understanding where an explosion may happen in the facility, implementing ignition prevention systems, following rigid housekeeping standards, and providing proper employee training should all be part of designing a process to minimize the threat of an explosion starting. Employing such measures as explosion venting, suppression and isolation, will minimize the risk of an explosion in process equipment from escalating into a catastrophic event in the facility.