Materials Testing
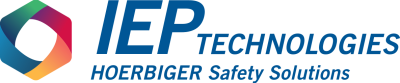
Materials testing is the first step
breadcrumb >> list
The Right Suppression System for Your Company
An explosion suppression system consists of three components: a detector; control unit; and suppressor(s). In the event an ignition occurs, the fireball expands from the ignition kernel with the pressure wave (created by the increase in temperature) traveling ahead of the flame front. Explosion pressure detectors are configured to respond to the characteristic pressure increase within milliseconds.
The explosion suppression control unit receives the detection signal from the pressure sensors and sends a release signal to the explosion suppressor(s). Suppressant is injected into the protected vessel at high rate and high velocity, using specially designed nozzles to disperse the suppressant and engulf the growing fireball. This rapidly cools the fireball, mitigating further combustion and reducing the explosion pressure. Integral to the design of most explosion suppression system is a chemical or mechanical explosion isolation systems to reduce the risk of flame/explosion propagation to other connected process equipment.
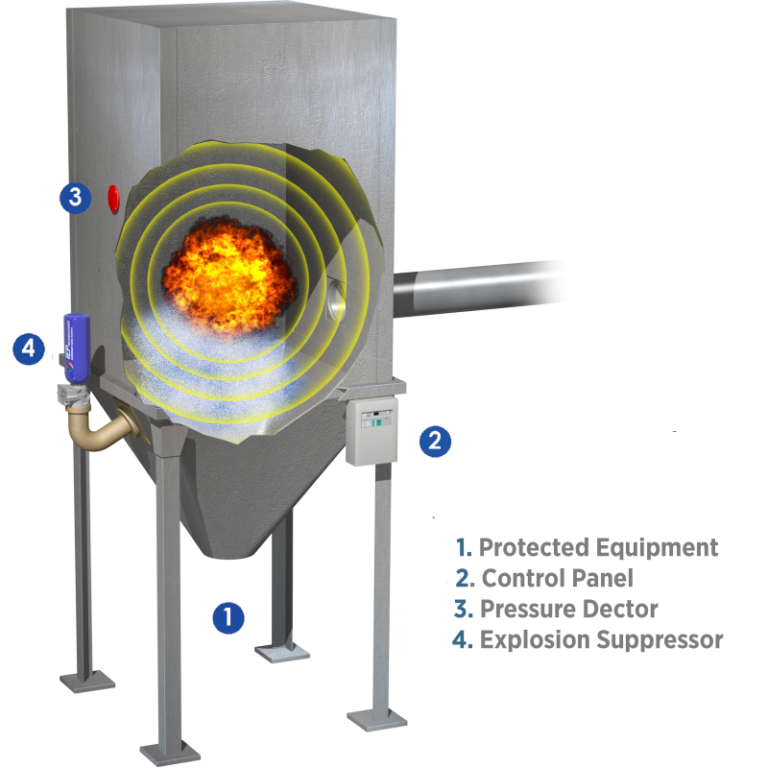
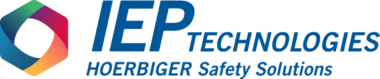
The First Step to The Right System
The first step in determining the right suppression system for your application is to know what you are dealing with.
Capt-Air has access to IEP Technologies Combustion Research Center and can determine the combustion properties of your process materials, singly and in combination.
The types of determinations we can make are as follows
Dust cloud explosibility data
Minimum explosible concentration
MEC may be used as an element of a deflagration risk assessment that takes into account all of the factors that are pertinent to an assessment of the explosion and fire hazard of a particular process.
Limiting oxygen concentration
LOC of a dust can be of value when developing fire and explosion prevention and protection strategies that employ inert gases to reduce the concentration of oxygen in a processing space.
Minimum ignition energy
MIE of a dust cloud is primarily used to assess the likelihood of ignition during processing and handling. The likelihood of ignition is used to evaluate the need for precautions such as explosion prevention systems.
Ignition temperature of a dust cloud
MIT of a cloud measures the minimum temperature at which a given dust cloud will auto-ignite when exposed to air heated in a furnace at local atmospheric pressure.
Hot surface ignition temperature of a dust layer
MIT of a layer measures the minimum temperature at which a dust layer will self-heat. This dust ignition characteristic can be used as one element of a fire risk assessment that takes into account all pertinent risk factors.
Ignition by self heating
Is a procedure to assess the tendency of a bulk dust to undergo spontaneous ignition when exposed to a heated environment.