Advances in Active Explosion Suppression Systems
Active Programmable Detectors & Controllers
breadcrumb >> list
Article reprinted from IEP Technologies link
Mitigating Industrial Explosion Risks
Explosion - Ever Present Threat
Industrial dust explosions pose an ever-present threat within many processing industries worldwide. Such events can have destructive results that can lead to business interruption, plant destruction, injuries, and even fatalities. A range of well-established protection measures are available and commonly used across the globe to mitigate against the industrial explosion risk.
Active Explosion Suppression
One such method is active explosion protection. Active explosion protection systems are designed to monitor process conditions to detect deflagrations and rapidly intervene to suppress developing explosions and prevent them from propagating to interconnected plant and equipment. Active protection systems were introduced more than 70 years ago and are generally referred to as explosion suppression and chemical- or mechanical-based explosion isolation systems.
Problems with Active Explosion Suppression
Despite the documented success of these protection measures in terms of reducing business losses and enhancing personnel safety, certain undesirable consequences have occasionally been associated with active protection, particularly inadvertent or “nuisance” activations. These nuisance activations can result in production downtime and product/material losses, so as advances in explosion protection technology have emerged, new techniques are being developed to address this issue and provide a more reliable protection solution for the end-user.
Improvements in Active Explosion Suppression
There are four key areas in active explosion protection where the greatest improvements can be seen:
- System design methodology
- Detection technologies for reliability and performance
- Electromechanical explosion suppressors
- Advances in control unit technologies
System Design Methodology
Traditional Design Methodologies
Traditionally, explosion protection system design has been based on a volume and concentration-dependent design approach focusing on calculations made from explosive dust concentration and vessel/equipment volume. However, there are many other process, material, and equipment hazard variables that should be considered when designing an explosion protection system. Some of these items include the explosivity characteristics of the combustible dust/vapor, geometry of the vessel, length of agent throw, detection threshold, orientation of the extinguisher discharge plane, and efficiency of the agent and discharge nozzles. Considering the effects of these variables will have a significant impact on the system design and calculated reduced pressure after suppression (PRED).
Advancements with CAD
Recent developments in computer-based modeling have resulted in design tools that enable a more thorough analysis of the proposed protection scheme for both explosion suppression and explosion isolation systems, based on both optimum conditions and those more challenging such as lean dust-air explosions, multiple ignition location scenarios, and suppression agent and extinguisher efficiencies, while taking also into account a broadening range of detection technologies.
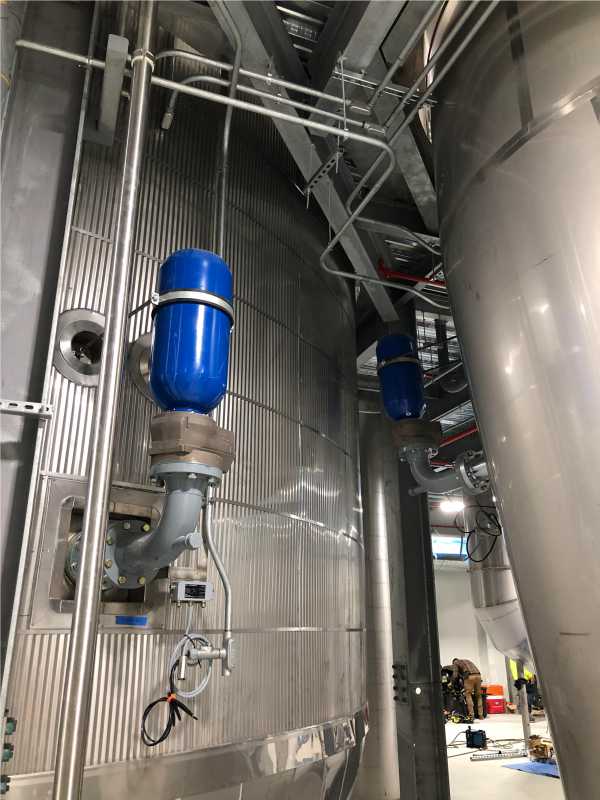
Advancements in Detection Technologies
Problems with Nuisance Activation
When a nuisance activation occurs, it is most often due to process pressure imbalances and the use of single set-point static pressure detectors that have inherent limitations.
Historically, the typical explosion suppression system has included these older technology “static” pressure detectors that require field configuration during system set-up as well as periodic recalibration. However, these types of detectors can be prone to triggering activations due to unexpected process pressure upsets and unforeseen fault conditions.
Programmable Pressure Detectors
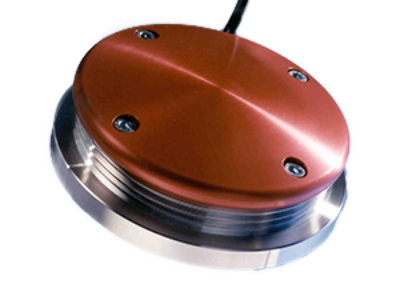
More recent advances have led to the introduction of programmable dynamic “rate of rise” detectors. The use of dynamic explosion detection has substantially reduced false alarms due to process pressure variations. Some of the more advanced dynamic detectors are now available incorporate data capture and a memory buffer, which enables application-specific programming prior to start-up, simulating faulty equipment/components and normal/abnormal process scenarios. A significant benefit of this data capture is the ability to review pressure-time graphs when performing a post-event analysis, to confirm the successful suppression and aid in understanding the timeline as the operations team works to determine the source of the ignition.
Improved IR Detectors
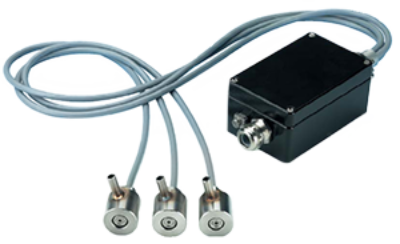
Infrared (IR) detectors are now providing complementary design options, either as a stand-alone device or in combination with pressure detectors, to provide a more effective overall detection solution, especially in challenging applications where it is desirable to optimize the explosion isolation distance on inlet and exhaust ducts. A good example of this is where the protected application includes an inlet duct to a large volume handling a product with a relatively low explosivity index. In this situation, the IR detector can provide a secondary level of assurance by detecting a flame already propagating into the duct, ahead of a relatively slow rate of pressure rise that has not yet reached the pressure detection threshold.
Combining Detectors
A combination of IR and pressure detection offers greater flexibility in isolation barrier locations, and greater dependability in achieving effective isolation under a wider range of deflagration propagation scenarios.
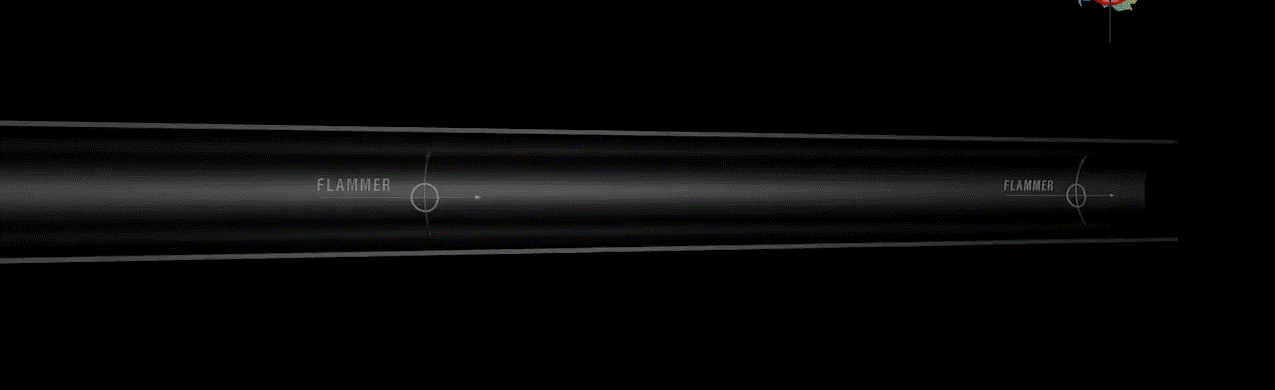
Advances in Control Unit Technologies
In any comprehensive explosion protection solution, all the discreet elements of the system are linked back to a control unit that provides the “brains” of the system.
In recent years, units have progressed from standard single point controllers through to micro-processor based multi-zone units, with the ability to provide many discreet zones of protection. Some of today’s control units are programmable, have self-testing and with digital display of fault/alarm conditions allowing easy diagnostics. The zoning capability brings practical benefits and cost savings to users, including installation flexibility and enabling the related explosion protection measures to be activated selectively. Features also include event history with date/time stamp for analysis, as well as enhanced communication capabilities, interfacing with process and plant control systems and alarms.
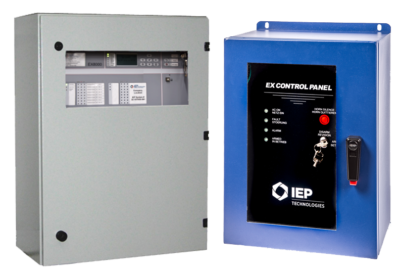
Summary
Recent advances in active explosion protection technologies are protecting process, plants, and people in ever more innovative ways, while providing users with greater functionality and practicality, including:
- Design tools factoring in many different process parameters, with individualized results
- Dynamic explosion detection with history buffer
- IR detection for interconnected ducting
- Electromechanically operated extinguishers with functionality testing capability, full diagnostics, and integrated safety features
- Multi-zone control units with LED/LCDs for status, diagnostics, multiple outputs, self-test diagnostics
This pace of change is likely to continue as more research and development is focused on this vital area to bring yet more intelligent industrial explosion protection to the worldwide processing industries, with the joint goals of improving safety while minimizing business interruption costs.